PakScan is a non-destructive, multi-product seal integrity tester for pouches, sachets and flexible packaging.
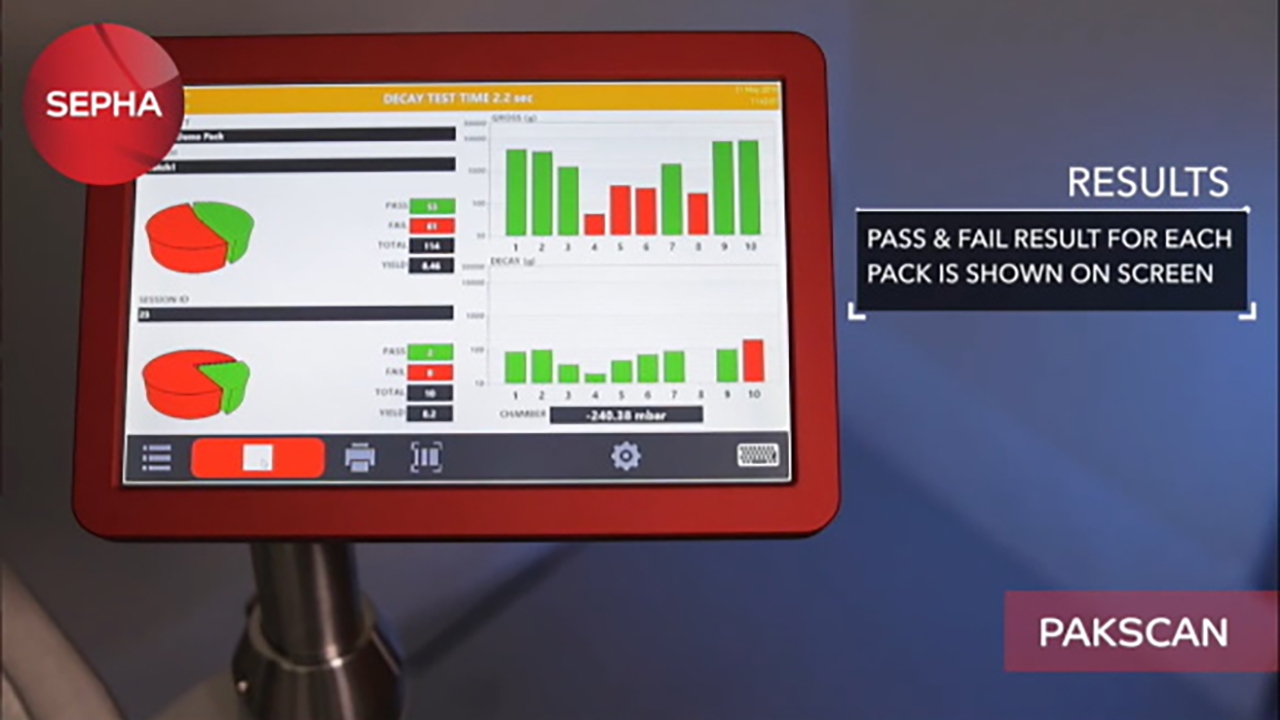
Using force decay technology, the Sepha PakScan is a non-destructive, multi-product seal integrity tester developed to verify package integrity of non-porous flexible packaging.
The machine offers a clean and dry leak detection test solution for modern manufacturers and packaging companies that pack dry product in pouches, sachets, bags and stick packs containing dry powder or solid components/medical devices.
The Sepha PakScan is a non-destructive test method. The machine performs a dry seal integrity test enabling manufactures to recover packs that have passed the leak test and return them to the production line.
The system can identify gross holes, leaks and weak seals down to 10μm* in up to 10 packs simultaneously within 30 seconds. The method provides deterministic and objective results, visualised on the result screen via a pass or fail for each individual packet. The software is developed in line with FDA 21 CFR Part 11 regulations enabling manufactures to store and export data for audit purposes, while protecting reports from being edited or deleted.
* Pack and material dependent
The Sepha PakScan is suitable for flexible packaging made from non-porous material including PVC, PVDC, Aclar and Aluminium foils and laminates. The system offers standard configurations to include 3, 4, 5, 6, 8 or 10 packs and can be customised to accommodate larger packs. The table below shows the different pack sizes per configuration:
Configuration | Length (mm) | Width (mm) | Thickness (mm) |
---|---|---|---|
3 Packs | 270 | 155 | 45 |
4 Packs | 270 | 95 | 45 |
5 Packs | 270 | 95 | 45 |
6 Packs | 130 | 155 | 45 |
8 Packs | 130 | 95 | 45 |
10 Packs | 130 | 95 | 45 |
-
Features
- Non-destructive seal integrity and leak detection device that uses force decay technology to detect weak seals and holes down to 10µm (pack and material dependent)
- Can test up to 10 packs simultaneously (standard configurations: 3, 4, 5, 6, 8 & 10 packs)
- Capable of handling dry, non-porous packages
- User defined password protection ensuring multiple operator use
- Easily validated system
- Repeatable test with deterministic and objective pass/fail results
- Test results can be printed, exported via USB (2x) or integrated into local quality control system via Ethernet cable
- Active Directory and OPC connectivity available on request
- System can be run in compliance with 21 CFR Part 11
-
Technical Spec
- Pack Type
Sachets, pouches, bags and MAP (flexible, non-porous materials) - Pack Size
See table in Features - Test Cycle Time
From 20 secs. - Measurement Ranges
Down to hole size of 10 micron (pack and material dependent) - Operation
Semi–automatic - Machine Construction
304 Stainless Steel Workstation, Anodised Aluminium Test Area. All product contact areas are cGMP. - Utilities
– Electrical: 110/230V Single Phase AC 50/60Hz – Air: Min. 20L/min at 0.6Mpa [ISO8573-1:2010 CLASS 2] - Configuration Options
2x USB Ports, 1x Ethernet Port
- User Interfaces
12.1 inch HDMI resistive touchscreen (1280 x 800 resolution) - Tooling Changeover
Approx. 1 minute - Audit Compliance
System can be run in compliance with 21 CFR Part 11 - Machine Dimensions (excl. screen)
670mm (L) x 760mm (W) x 882mm (H) - Machine Dimensions (incl. screen)
670mm (L) x 1042mm (W) x 1195mm (H) - Machine Weight
200kg - Shipping Weight
260kg - Warranty
Supplied with a 12-month warranty. (Extended warranties are available for additional support).
- Pack Type
-
Application
Drug stability testing in laboratories
R&D departments test materials to ensure the correct materials are used to protect new products from contamination by moisture, air and bacteria.
QA Testing of packaging processes
Build leak tests into the Quality Assurance procedures for your packaging line. Objective seal testing ensures the integrity of the packaging process.
Reduce production rejects
Minimise reject pouches and sachets and waste disposal created in pharmaceutical production and packaging facilities by carrying out leak testing more frequently. Earlier detection of a leak means line operators can troubleshoot the cause of a leak before a large volume of faulty packages are produced.
-
Benefits
Non-destructive test generates less waste and bigger product yield
- The non-contact method is clean and dry, unlike destructive leak testing methods (e.g. Methylene Blue Dye Test) and does not destroy test product or packaging.
- Tested product can be retrieved from faulty packs and repackaged.
- Packs which pass the leak test can be put back onto the production line.
Accurate, validated results for each pouch or sachet
- Detects holes down to 10 microns.
- Automatically stores product-specific data in pre-designated file locations. PakScan verifies the product to be tested before each cycle.
- Totally objective results as no operator intervention is required
- Pass or fail criteria can be set to the same micron level as your existing Methylene Blue Dye Test.
- Result data is stored and can be printed or downloaded to other storage devices for further analysis.
Quicker troubleshooting for line set-up to reduce rejects
- Fast test cycle means that leak testing can be carried out more frequently.
- Earlier detection of leaks allows line operators to investigate the cause of the failed seal more quickly, so fewer faulty packs are produced on the line.
Easy to use
- No special technical skills required.
- Touch screen operator interface.
- 1 Minute product changeover.
-
Force Decay
How does Force Decay testing work?
A flexible package is placed within a tool set which comprises of a strain gauge load cell, which in turn is housed within a vacuum test chamber.
Vacuum is applied to the test chamber and under this vacuum the flexible package will expand and generate an expansive force in response to the vacuum.
The strain gauge load cell measures the expansive force over time to determine if the package has a gross leak, micron leak or has no leaks.
- If there is a gross leak, no expansive force is measured.
- If there is a micron leak, an expansive force is initially measured but will start to reduce over time as the pack lets air escape into the vacuum chamber.
- If the pack is good it will expand under vacuum and remain inflated and in turn generate a constant force measurement over time.
To ensure the integrity of the pack is not affected or does not burst, a force reaction/restraining plate is used to prevent full expansion.
Learn more